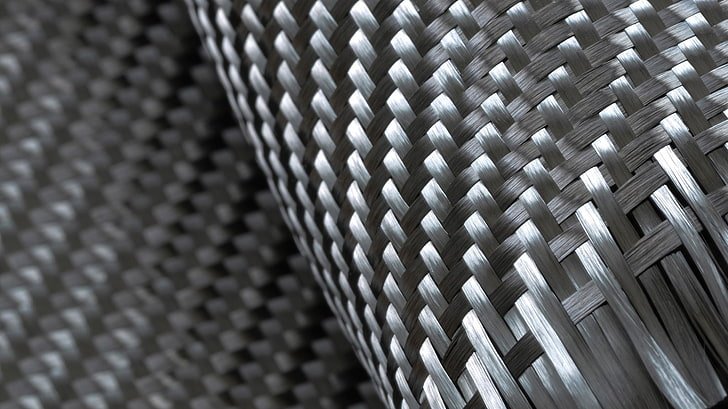
carbon - faq’s - answered
why buy a carbon fiber helmet?
Carbon Fiber is renowned for its high strength to volume ratio. Depending on the orientation of the fiber, a carbon fiber composite can be stronger in a certain direction or equally strong in all directions. A small piece can withstand an impact of many tons and still deform minimally. The complex interwoven nature of the fiber makes it very difficult to break.
I know carbon fiber helmets are lighter, but is it that important?
From Stilo…
”To take you back to high-school physics for a moment, you might remember the equation: weight = mass x gravity. Formula 1 (F1) cars pull at least 4gs when cornering. With that in mind, it’s easy to see how, under cornering loads, a helmet with a mass of a little over 2.5 pounds suddenly weighs more than 10 pounds, putting huge force on the driver’s neck. As a result, even reducing the mass by a couple of ounces adds up to a valuable weight saving.”
Even minimal weight reduction aids driver comfort and reduces neck fatigue - consequently enhancing their performance. This is particularly true for endurance racers. Our customers have confirmed this.
Weight reduction is even more relevant for junior drivers’ necks and shoulders, whose frames and muscles are not fully developed to withstand the rigors of motorsports.
are carbon fiber helmets stronger?
Yes, carbon fiber helmets are stronger than fiber glass helmets or composite helmets but there’s more…
Carbon fiber has an unrivalled strength-to-weight ratio. Stronger than steel yet significantly lighter than aluminum or fiberglass.
Carbon fibers are made from a very large number of fine, high-strength fibers than are woven together in various formats producing an exceptionally strong material. Certain weaves (twill, harness satin) create a flexible, light, strong material that can be draped and excellent for forming over complex shapes.
The increased strength of carbon fiber helmets with the decreased weight allows manufacturers to decrease the thickness of the shell allowing them to increase the depth of the interior crush and comfort padding.
In addition, the characteristics of carbon fiber makes it even more relevant to drivers’ increased safety and performance this includes…
Superior Impact Protection: Carbon fiber (unlike the composites or fiber glass) does not crack - it bends. The tightly woven fibers (see below) create a rigid structure that resists penetration and deformation. On impact, the force dissipates and is absorbed over a wider area. A severe crash may result in micro cracking of the shell, but not a penetrating open crack.
Reduced Rotational Forces: What does this mean? Think concussions.
A lighter helmet experiences less inertia during rotational impacts, which are increasingly understood to be a major cause of concussions and other brain injuries. By minimizing the helmet's mass, carbon fiber helps to limit these damaging rotational accelerations.Durability and Longevity: Carbon fiber is a very durable material that resists degradation from environmental factors like UV radiation and moisture. Under normal use a carbon fiber shell can maintain its structural integrity for longer periods compared to other materials. The carbon fiber shell certainly better survives the normal abuse helmets receive while at the track - especially the hits from entering/exiting the car.
Improved Aerodynamics: The properties inherent in the carbon fiber weave allows the smooth integration of aerodynamic features for open cockpits. In addition, the ability to alter the finish has proven aerodynamic advantages - especially at high speeds.
Other relevant properties beyond a high strength to weight ratio: Rigidity, corrosion resistance, electrical conductivity, fatigue resistance, good tensile strength but Brittle, fire resistance/not flammable, non poisonous, biologically inert, x-ray permeable…
What about the weave? Are some better than others?
Remember Snell SA and FIA 8859 homologated helmets have undergone (and passed) rigorous testing. To meet the even more stringent strength testing FIA 8860 helmets have to sport a carbon fiber shell.
The weave used by manufacturers is more to do with aesthetics, costs, drapability plus branding than increased safety factors.
Carbon fiber manufacturing is complex with many variables. To simplify, carbon fibers or filaments are formed then bundled together into what are called TOWS. Tows are identified by the number of carbon filaments they contain. For example, a 3k (common standard) tow contains 3,000 carbon filaments and is just .125” wide! This density of filaments gives carbon its strength.
The tows are then woven to form sheets of carbon fiber fabric. And how they are woven produces variables from a high level of stability (stiff) to pliability. The most common weaves created are plain, twill, and harness satin. Twill and harness satin tows are more likely to be used in helmet manufacturing because they can be draped.
Plain weave, is slightly stronger, as the patterns are more tightly packed. This is ideal for carbon fiber applications where structural integrity is paramount. A plain weave carbon fiber sheet looks symmetrical with a small checkerboard style appearance. Generally, plain weave fabrics are suited for flat sheets, tubes and 2D curves
Twill weave: Twill patterns, with its slightly looser weave, have slightly less load-bearing capacity but more formability than the plain weave.
A twill weave is formed by tows passing over a set number of tows then under another sets of tows. This over/under process creates a diagonal arrowhead look. As the 2×2 name implies, each tow will pass over 2 tows then under two tows. Similarly, 4×4 Twill will pass over 4 tows then under 4 tows. Any larger number increases formability because the weave is not as tight, but this does decrease its stability.
Harness Satin Weave: Satin weaves have been used for thousands of years to give silk fabric its beautiful draping quality while leaving the fabric smooth and seamless. When used with carbon fiber composites, satin weaves translate to an ability to easily form around complex contours. However, this also means satin weaves offer less stability than other weaves.
The most common harness satin weaves are four harness satin (4HS), five harness satin (5HS), and eight harness satin (8HS). The number indicates the total number of tows passed over then under
Harness Satin weaves produce distinct, aesthetic patterns which manufacturers love to use to both distinguish their brand and even between models.
Why are some carbon fiber helmets distinctly more expensive that others?
Not all carbon helmets are true carbon fiber helmets. The less expensive helmets may have composites shells with a carbon fiber outer layer. This is usually revealed in the manufacturers description.
Manufacturing process. Major brands, especially those that also manufacture their helmets (Bell, Schuberth, Stilo) have state-of-the-art research and production facilities with experience skilled employees. This allows the brand to control the process, the techniques, the characteristics, introduce designs that maintains quality, consistency, introduce their innovation to consistently produce the best, pro-racing carbon fiber helmets.
Other brands have outsourced the production of their helmets. This can lower the price, but the manufacturer may be using older manufacturing techniques often produce helmets that are not as light or have the meticulous layering and resin infusion techniques to achieve the optimum strength, look and quality.
https://www.elevatedmaterials.com/carbon-fiber-weaves-what-they-are-and-why-to-use-them